Traditional injection molding
It allows to create products with medium-small thicknesses. Use of materials with uniform colours added with mineral and fibrous fillers and/or reinforcements.
Gas assisted injection molding: GAIM
Co-injection of pure nitrogen inside the plastic material and emptying of the piece.
Production of extremely resistant and light articles.
Further advantages are:
- Better aesthetic appearance free from shrinkage;
- Dimensional stability, compaction, and flatness at the highest levels;
- Faster molding cycles thanks to the lower thickness of plastic material to be cooled;
- Material savings and lighter products;
- Use of presses with lower tonnage than the traditional one;
- Savings in energy consumption of 20 to 30% with each cycle
Bi-material and tri-material over-injection molding
Use of bi-material presses which offer the possibility of molding two different thermoplastic materials in the same mold, thanks to two independent injection groups.
Advantages:
- eliminate assemblies and reduce cycles;
- produce products in two or more colours;
- overmold sealing gaskets of various types;
- produce high thickness products;
- improve the tactile perception of the product;
Molding techniques available:
- Transfer system
- Rotary table system
- Index plate system
- Sliding split system
Co-injection
Possibility of molding a product using recycled or regenerated post-consumer material and further covering with material of higher aesthetic quality.
Injection molding with metal insert
Insertion of metal accessories directly into the mold cavity, which are incorporated into the molded plastic product.
Type of materials
Polymers: PVC-U, ABS, PP, PE, PS.
Techno polymers: POM, PA6, PA66, PBT, PC, PPA, PMMA, TPE.
Super polymers: PPS, LCP, PARA.
Casagrande s.r.l.
- 20 injection presses from 40 to 500 tons
- 1 dual-material press
- 6 presses equipped with gas injection technology
- 3 fully electric presses: 100 / 300 / 400 tons
- 2 Engel Victory (without columns)
- 1 External auxiliary injection equipment
- 4 “Kawasaki RS 20 and RS 10” robots
- 13 Cartesian robots
- injection molding operates 24 hours a day (three shifts per day), peak season 7 days a week
Total molding area: 2,000 m²
Dizeta Slovakia s.r.o.
- 14 injection presses from 50 to 400 tons
- 6 Engel Victory (without columns)
- 1 External auxiliary injection equipment
- 14 Cartesian robots
- Assembly lines
- injection molding operates 24 hours a day (three shifts per day), peak season 7 days a week7
Total molding area: 2.000 m²
Pad printing
2 colors
Other finishes available
We are supported by qualified external suppliers for the execution of various types of surface finishes such as:
- metallization
- chrome plating
- pad printing (+2 colours)
- screen printing
- water transfer printing
- painting
- sticker application
Quality control
Quality control starts from the early stages of acquisition and analysis to guarantee compliance with ISO 9001 and IATF 16949 standards.
Measurement and quality control tools we have:
- Microbalance
- Thermobalance (humidity meter)
- Spectrophotometer
- Luximeter
- Profiles projector
- Creation of certified control templates
- For further analyses we have the external support of IEC17025 certified laboratories
Inline assembly
Welding
Our Best Clients
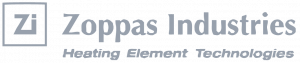
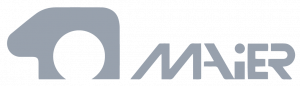
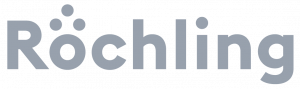
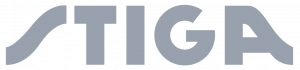
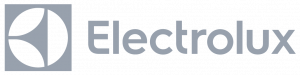
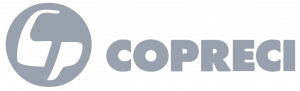
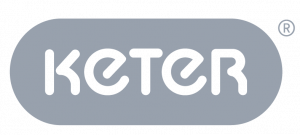

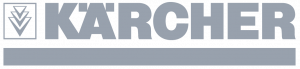

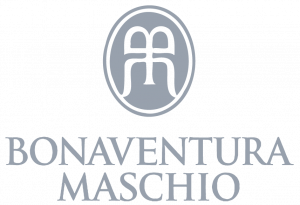
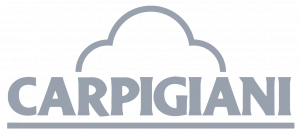
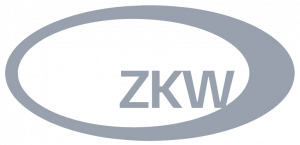
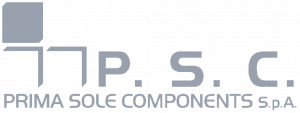
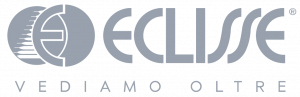
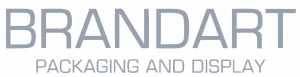
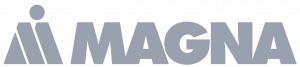
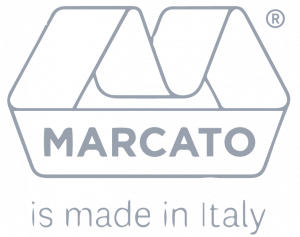
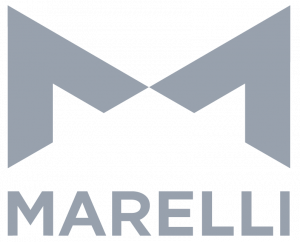
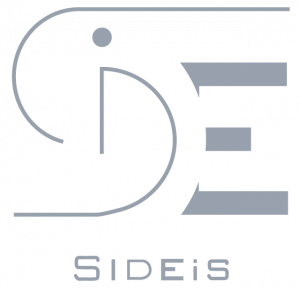